High Precision Injection Moulding: Transforming Manufacturing for the Future
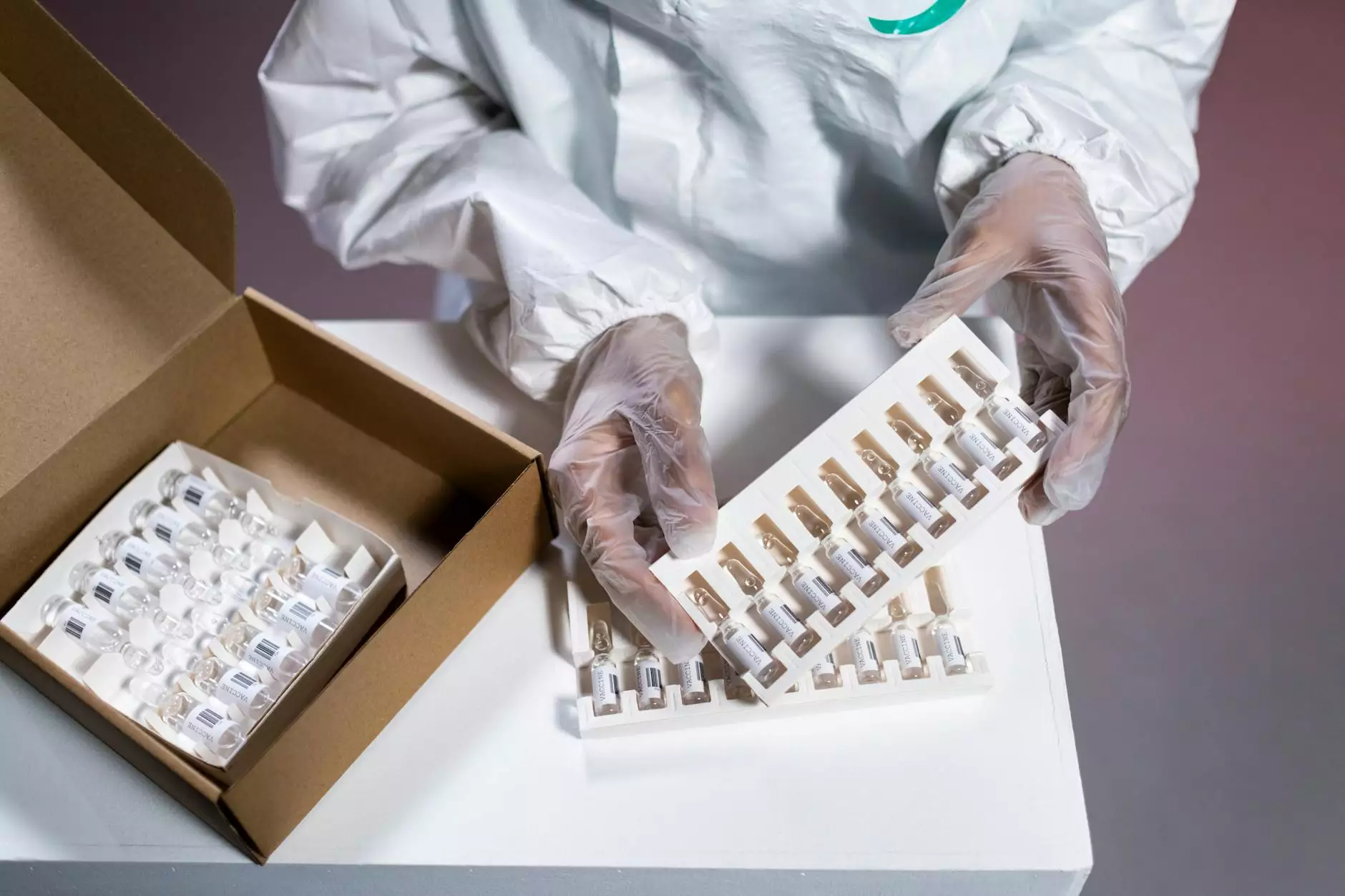
High precision injection moulding is an integral part of modern manufacturing, revolutionizing the way products are produced across various industries. It combines cutting-edge technology with precise engineering to deliver exceptional quality and efficiency. In this article, we will explore the fundamentals, advantages, applications, and advancements in high precision injection moulding, and how businesses like Deep Mould are leading the charge in this dynamic field.
Understanding High Precision Injection Moulding
At its core, high precision injection moulding is a manufacturing process that involves creating parts by injecting molten materials into a mould. The precision aspect is key, as it entails producing components that meet stringent tolerances and specifications. This method is commonly used with a variety of plastics and metals, enabling businesses to create complex geometries with unparalleled accuracy.
The Process of High Precision Injection Moulding
The process of high precision injection moulding generally involves several critical steps:
- Material Preparation: Raw materials are prepared and fed into the injection machine.
- Melting: The material is heated until it reaches a molten state.
- Injection: The molten material is injected into a precision-engineered mould.
- Cooling: The material cools and solidifies within the mould.
- Demoulding: The mould is opened, and the finished part is ejected.
- Finishing: Any necessary post-processing is done to improve product quality.
Advantages of High Precision Injection Moulding
Investing in high precision injection moulding brings several significant advantages for manufacturers, including:
- High Tolerance: This method allows businesses to produce components with very tight tolerances, often within a few microns.
- Complex Shapes: With precision moulding, intricate designs that were once difficult or impossible to create can now be easily achieved.
- Reduced Waste: The efficiency of this process minimizes material waste, leading to more sustainable manufacturing practices.
- Faster Production Rates: High-speed cycles mean that manufacturers can produce parts at a remarkable pace, reducing overall lead times.
- Cost-Effectiveness: While the initial setup costs can be high, the long-term savings in material and production efficiency can provide a solid return on investment.
Applications of High Precision Injection Moulding
The versatility of high precision injection moulding makes it applicable across a range of industries, including:
- Automotive: Creating precise parts for engines, dashboards, and other critical components.
- Medical: Producing intricate devices and components for medical applications with stringent regulatory requirements.
- Aerospace: Manufacturing lightweight and robust components that can withstand extreme conditions.
- Electronics: Facilitating the production of housings, connectors, and other parts for electronic devices.
- Consumer Goods: Enabling the design and production of diverse products that are visually appealing and functional.
Innovations in High Precision Injection Moulding
The field of high precision injection moulding is continuously evolving, with advancements in technology playing a pivotal role. Some notable innovations include:
- Smart Moulds: Incorporating sensors and IoT technology into moulds helps monitor conditions in real-time, ensuring optimal production environments.
- 3D Printing in Mould Design: Utilizing 3D printing technology in the creation of moulds allows for faster prototyping and experimentation.
- Material Advancements: Development of new materials that offer improved properties, such as enhanced strength and durability, expanding the applications of injection moulding.
- Automation and Robotics: Incorporating robotics into the injection moulding process improves accuracy and efficiency, allowing for high-volume production with minimal human intervention.
- Environmentally Friendly Materials: Innovations in sustainable materials have led to a rise in eco-friendly options that maintain precision while reducing environmental impact.
Challenges in High Precision Injection Moulding
While high precision injection moulding offers many benefits, it also presents some challenges that manufacturers need to navigate:
- Initial Setup Costs: The investment in high-precision machinery and mould design can be significant, making it essential to balance costs and expected returns.
- Technical Expertise: Successfully running high precision injection moulding processes requires skilled personnel who understand advanced manufacturing techniques.
- Material Limitations: Not all materials perform equally well in precision moulding, necessitating careful selection based on the application.
- Design Complexity: While complex designs can be achieved, they often require intricate moulds that can complicate the production process.
The Future of High Precision Injection Moulding
The future of high precision injection moulding looks promising, as industries continue to seek innovative ways to enhance production capabilities. With advancements in technology and growing demand for high-quality manufactured parts, we can expect:
- Integration of AI: Artificial intelligence will play a vital role in optimizing processes, predicting maintenance needs, and improving overall efficiency.
- Customization: Personalization trends are driving demand for customized solutions, and precision moulding can meet these needs effectively.
- Global Expansion: As more businesses recognize the benefits, the application of high precision injection moulding is set to grow globally across various sectors.
- Focus on Sustainability: With increasing awareness of environmental impacts, the adoption of sustainable practices and materials in injection moulding will continue to rise.
Choosing the Right Partner for High Precision Injection Moulding
To fully leverage the possibilities of high precision injection moulding, partnering with an experienced provider is crucial. Here’s what to consider:
- Technical Expertise: Ensure the partner has a deep understanding of precision engineering and material science.
- Advanced Technology: Look for companies that invest in state-of-the-art equipment and innovations.
- Quality Assurance: Strong quality control measures should be in place to meet and exceed industry standards.
- Customer Support: A reliable partner should offer excellent support throughout the project lifecycle, from design through production.
In conclusion, high precision injection moulding is not just a manufacturing method; it’s a significant advancement in production technology that is shaping industries around the globe. From automotive to medical, the ability to create high-quality, complex parts with minimal waste and maximum efficiency is ushering in a new era for manufacturers. By focusing on innovative solutions and sustainability, companies like Deep Mould are poised to remain at the forefront of this exciting field, setting new standards for what is possible in modern manufacturing.