The Revolution of Silicone Rubber Injection: A Game-Changer in Electronics and Medical Supplies
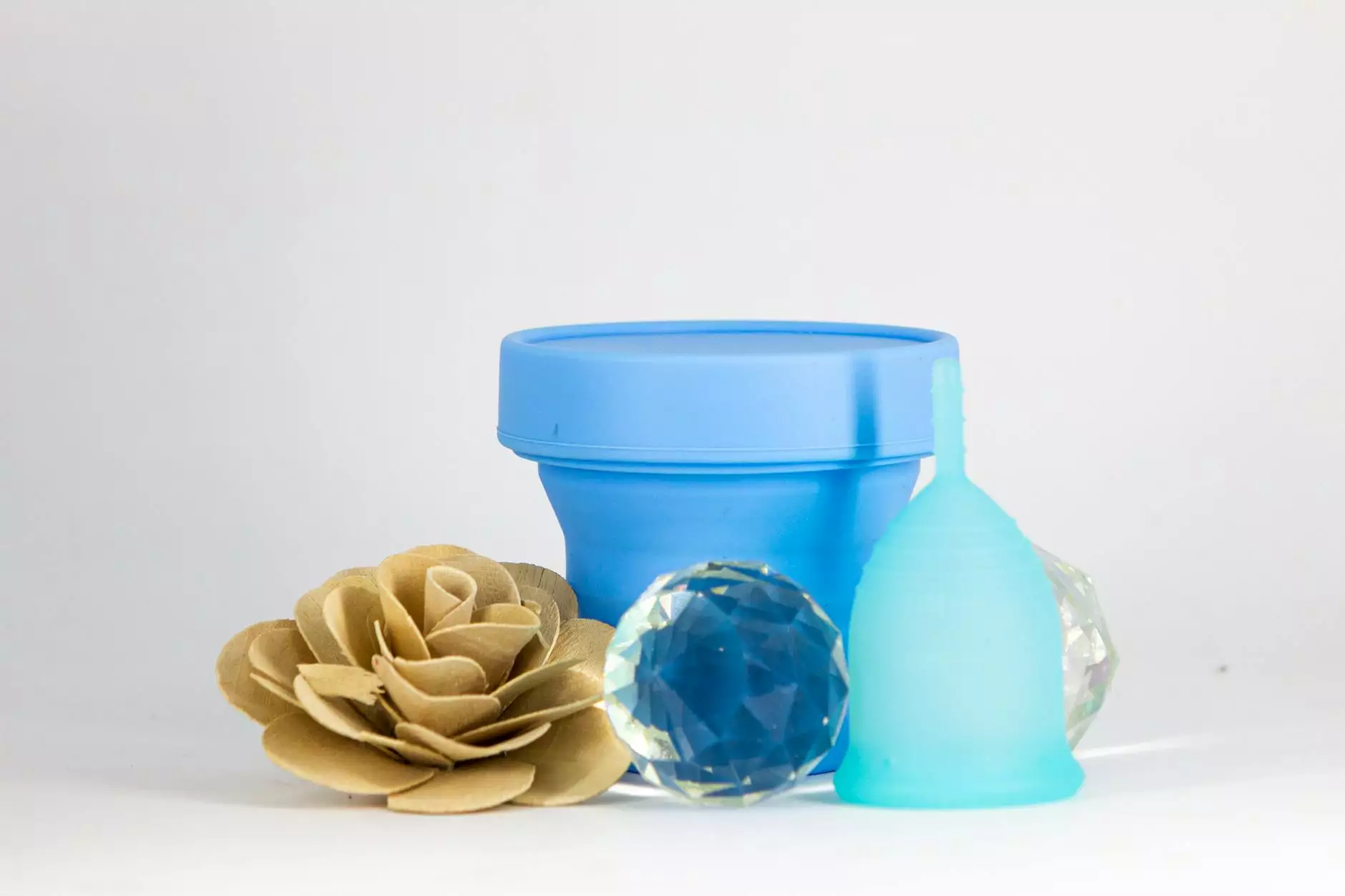
Silicone rubber injection molding has become an essential process in various industries, particularly in electronics and medical supplies. Its remarkable properties and versatility have made it the preferred choice for manufacturers seeking durable, reliable, and high-quality components. In this article, we will delve deep into the world of silicone rubber injection, exploring its benefits, applications, and future trends.
What is Silicone Rubber Injection?
Silicone rubber injection is a method used to manufacture components from silicone rubber, a synthetic material known for its elasticity, resilience, and temperature resistance. This process involves injecting liquid silicone rubber into a mold, where it cures to form solid shapes. This method is favored for its ability to produce intricate designs with high precision, making it ideal for applications in both the electronics and medical sectors.
Benefits of Silicone Rubber Injection
Understanding the benefits of silicone rubber injection is crucial for manufacturers and businesses considering this technology. Here are some of the key advantages:
- Durability: Silicone rubber is renowned for its ability to withstand extreme temperatures, UV exposure, and harsh chemicals. This makes it an excellent choice for products requiring longevity.
- Flexibility: The elasticity of silicone allows for easy handling and manipulation, enabling the creation of complex designs without compromising strength.
- Biocompatibility: Medical-grade silicone rubber is hypoallergenic and can be sterilized, making it suitable for use in medical devices and implants.
- Electrical Insulation: Silicone rubber provides excellent insulation, making it ideal for electronic components and devices.
- Low Maintenance: Silicone rubber components require minimal maintenance, reducing long-term operational costs.
Applications of Silicone Rubber Injection
The versatility of silicone rubber injection allows for a wide range of applications, particularly in the electronics and medical supplies industries. Here are some key areas of application:
Electronics
In the electronics sector, silicone rubber injection is used to create components such as:
- Connectors: Silicone rubber provides excellent sealing capability, ensuring connectors are protected from moisture and dust.
- Keypads: The soft-touch surface and flexibility of silicone make it perfect for keypad manufacturing.
- Encapsulation: Silicone injection is used to encapsulate sensitive electronic components, protecting them from environmental damage.
- Insulators: Silicone's electrical insulation properties make it ideal for use in high-voltage applications.
Medical Supplies
In the medical field, silicone rubber injection plays a crucial role in the development of a variety of devices and supplies, including:
- Catheters: The biocompatibility and flexibility of silicone make it ideal for catheter manufacturing.
- Sealants: Silicone rubber is used to create sealants for medical devices that require airtight seals.
- Prosthetics: The softness and durability of silicone rubber provide comfort and functionality in prosthetic limbs.
- Baby Products: Many baby items, such as bottle nipples and pacifiers, use silicone rubber due to its safety and ease of cleaning.
Understanding the Silicone Rubber Injection Process
The silicone rubber injection process can be broken down into several key steps:
- Design: Engineers create a detailed design of the component, considering the necessary specifications and tolerances.
- Mold Creation: A mold is fabricated from durable materials capable of withstanding high temperatures and pressures.
- Injection: Liquid silicone rubber is injected into the mold, filling the cavity and taking on the desired shape.
- Curing: The silicone rubber cures within the mold, solidifying into the final product.
- Demolding: Once cured, the finished components are removed from the mold for quality inspection.
Quality Control in Silicone Rubber Injection
Ensuring quality in silicone rubber injection is paramount, especially in medical and electronic applications where reliability is critical. Key quality control measures include:
- Material Inspection: Checking the raw silicone material for impurities and compliance with safety standards.
- Curing Time Validation: Monitoring the curing process to ensure components are fully cured before removal from the mold.
- Dimensional Tolerance Measurement: Verifying that components meet specified tolerances using precision measuring tools.
- Functional Testing: Conducting functional tests on electronic devices to ensure they perform as expected.
- Biocompatibility Testing: For medical applications, testing must confirm the biocompatibility of the silicone rubber used.
Future Trends in Silicone Rubber Injection
The landscape of silicone rubber injection is constantly evolving, driven by technological advancements and market demands. Here are some trends to watch for in the near future:
- Smart Silicone Products: Integration of electronics within silicone products to create smart applications, such as wearables and IoT devices.
- Sustainable Practices: Increasing emphasis on sustainability is leading manufacturers to explore eco-friendly silicone materials and recycling methods.
- Customization: The demand for customized silicone products will continue to rise as manufacturers adapt to specific client needs.
- Enhanced Manufacturing Techniques: The use of advanced technologies, such as 3D printing, will augment traditional silicone rubber injection processes.
Conclusion
Silicone rubber injection is transforming the landscape of the electronics and medical supplies industries. Its unmatched properties, including durability, flexibility, and biocompatibility, position it as a reliable solution for manufacturers looking to produce high-quality components. As technology continues to advance, the future of silicone rubber injection holds immense potential, promising further innovations and opportunities for growth. Businesses like Nolato are leading the way by embracing silicone rubber technology, ensuring they remain at the forefront of their industries.
Embrace the Future with Silicone Rubber Injection
As industries evolve, embracing innovative solutions like silicone rubber injection can give businesses a competitive edge. By investing in this technology, companies can enhance product quality, reduce costs, and meet the growing demands of consumers in both electronics and medical supplies. Silicone rubber injection is not just a manufacturing process; it is a pathway to innovation and excellence.