The Impact of Injection Molded Plastic Manufacturers in Modern Industry
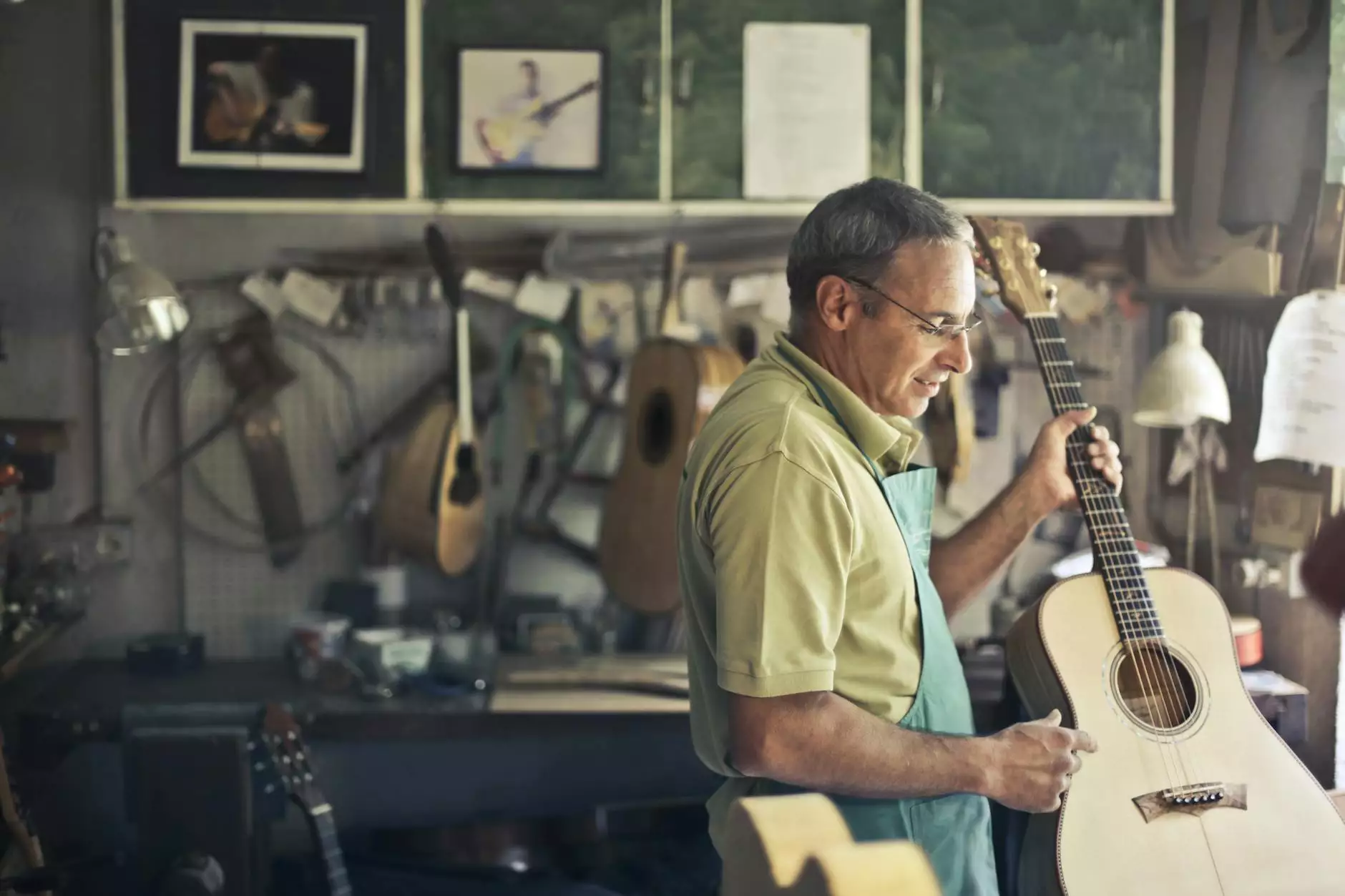
The world of manufacturing is evolving rapidly, and among the most significant players in this arena are injection molded plastic manufacturers. Their role has become pivotal in generating innovative products, reducing costs, and enhancing efficiency across numerous sectors. This article delves deep into the importance, processes, and benefits of working with these manufacturers, particularly within the category of Metal Fabricators.
What Is Injection Molding?
Injection molding is a manufacturing process used to produce items by injecting material into a mold. This sophisticated process is primarily employed with plastic but can also be adapted to metals and glass. The method itself involves several stages, including:
- Material Selection: Different types of plastics can be utilized, each offering unique properties.
- Mold Design: Creating a mold that will produce the desired shape and size of the end product.
- Injection: Heating the plastic until it melts and injecting it into the mold.
- Cooling: Allowing the material to cool and solidify in the mold.
- Finishing: Removing the finished part and performing any additional processes required to finalize the product.
The Advantages of Injection Molding
Injection molding offers numerous benefits compared to traditional manufacturing methods. Here are some key advantages:
- High Efficiency: Once the molds are created, large quantities of products can be produced quickly.
- Cost-Effectiveness: Ideal for mass production; the cost per unit decreases significantly when producing larger quantities.
- Design Flexibility: Enables the production of complex shapes that would be difficult or impossible to achieve with other methods.
- Material Variety: A wide range of plastics and additives can be used to tailor products to specific requirements.
- Reduced Waste: The injection molding process minimizes material waste compared to subtractive manufacturing methods.
Injection Molded Plastic Manufacturers: Key Contributors to Metal Fabrication
In the realm of Metal Fabricators, the collaboration with injection molded plastic manufacturers can lead to innovative solutions that combine the strength of metals with the versatility of plastics. Here’s how:
1. Enhancing Product Durability
By integrating plastic components manufactured through injection molding, metal products can be reinforced and protected against environmental factors that could lead to corrosion or wear. This dual-material approach is essential in industries such as automotive and aerospace, where durability is paramount.
2. Cost Reductions and Product Reformulation
Utilizing injection molding allows manufacturers to replace metal parts with lighter, less costly plastic parts. This can significantly reduce shipping costs, increase fuel efficiency, and lower overall production costs without compromising quality.
3. Accelerated Product Development
The rapid prototyping capabilities of injection molded plastic manufacturers enable Metal Fabricators to iterate designs quickly and bring new products to market faster than ever before. This agility is essential in today’s fast-paced industrial landscape.
Choosing the Right Injection Molded Plastic Manufacturer
When seeking the right injection molded plastic manufacturers, there are several critical factors to consider:
1. Experience and Expertise
The manufacturer’s experience matters. Look for companies that have a solid track record in the industry and have worked with similar products or materials. Experienced manufacturers are better positioned to overcome design and production challenges.
2. Quality Assurance Standards
Quality control is vital in the injection molding process. Ensure your chosen manufacturer adheres to recognized quality standards (like ISO 9001) and implements rigorous testing and inspection processes.
3. Advanced Technologies
Inquire about the technology utilized in the injection molding process. Advanced machinery and automation can enhance precision, reduce cycle times, and increase product consistency.
4. Customization Capability
The ability to customize molds and processes is essential. Discuss your specific needs and ensure the manufacturer is receptive to accommodating special requirements, whether they relate to size, shape, or materials.
5. Sustainable Practices
As environmental concerns grow, partnering with manufacturers that prioritize sustainability can significantly benefit your business. Look for practices that promote recycling and the use of eco-friendly materials.
Conclusion: The Future of Injection Molding and Metal Fabrication
As industries continue to evolve, the synergy between injection molded plastic manufacturers and metal fabricators will only deepen. This collaboration will lead to innovative products that not only meet current market demands but also anticipate future trends. By understanding the processes, benefits, and partner selection criteria, businesses can position themselves for sustained success in a competitive landscape.
In summary, the role of injection molded plastic manufacturers is essential not only in creating efficient manufacturing solutions but also in enhancing the overall performance and profitability of metal fabrication endeavors. Businesses must leverage these relationships to foster innovation, improve product performance, and achieve greater operational efficiencies.
For more information on high-quality injection molded plastic solutions and to partner with industry leaders, visit deepmould.net.