CNC Precision Machining Parts Factory: An In-depth Exploration
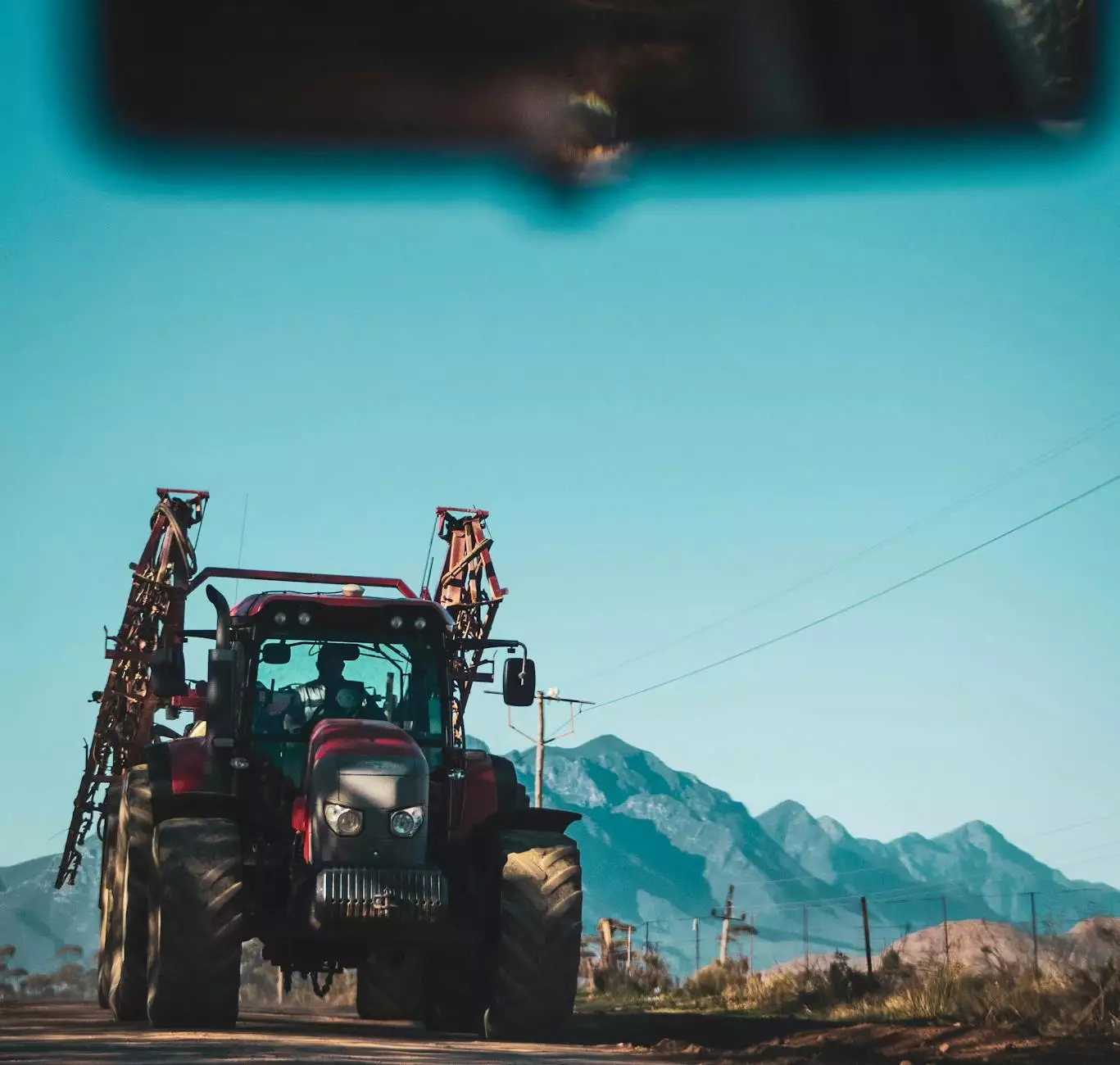
In today's fast-paced industrial landscape, the demand for precision and quality in manufacturing is at an all-time high. At the heart of this demand lies the cnc precision machining parts factory, a key player that integrates cutting-edge technology with expert craftsmanship to produce components that adhere to the strictest specifications. In this comprehensive article, we will delve deep into the world of CNC machining, exploring its benefits, processes, applications, and much more.
Understanding CNC Machining
CNC, or Computer Numerical Control, machining is a process that automates the control of machine tools through a computer. This advanced technology utilizes cutting tools to shape materials with extreme accuracy, allowing manufacturers to create intricate parts that meet demanding specifications.
Manufacturers can produce components from a variety of materials, including metals, plastics, and composites. The precision offered by CNC machining makes it a preferred choice for industries such as automotive, aerospace, medical, and electronics.
History of CNC Machining
The origins of CNC machining date back to the 1940s and 1950s when the first numerical control machines were developed. These early machines used punch cards to control their movements. As technology advanced, so too did the capabilities of CNC machines. By the late 20th century, the evolution of computer technology led to the sophisticated CNC machines we rely on today.
Benefits of CNC Precision Machining
There are numerous advantages to using CNC precision machining in manufacturing. Below are some of the most notable:
- High Precision and Accuracy: CNC machining offers unmatched precision. Parts can be produced with tolerances as tight as ±0.001 inches, making it ideal for industries that require exact specifications.
- Complex Designs: CNC machinery can produce intricate shapes and designs that would be virtually impossible to achieve with manual machining.
- Efficiency: CNC machines operate continuously without loss in speed or quality, resulting in high productivity and lower costs.
- Consistency: Once a program is set, the CNC machine can reproduce identical parts repeatedly, ensuring uniformity across batches.
- Material Versatility: CNC machining can work with a wide variety of materials, allowing for greater flexibility in design and manufacturing.
The Role of Metal Fabricators in CNC Machining
Metal fabricators play a crucial role in the CNC precision machining industry. They are responsible for transforming raw materials into ready-to-use components through a combination of cutting, bending, and assembling processes. At a cnc precision machining parts factory, metal fabricators contribute significantly to the overall efficiency and quality of production.
Metal fabricators must possess a detailed understanding of various metals, their properties, and how they interact during the machining process. Furthermore, having knowledge of the latest CNC technologies and techniques is essential for fabricators to stay competitive in the industry.
Key Responsibilities of Metal Fabricators
- Material Selection: Choosing the appropriate materials based on project specifications and end-usage.
- Design Interpretation: Reading and interpreting CAD (Computer-Aided Design) drawings to understand product requirements.
- Machine Operation: Setting up and operating CNC machines to fabricate parts according to exact specifications.
- Quality Control: Conducting inspections and tests to ensure each product meets quality standards.
- Maintenance: Performing regular maintenance and troubleshooting on CNC machines to ensure optimal operation.
Processes Involved in CNC Precision Machining
The CNC precision machining process encompasses several steps, each contributing to the production of high-quality parts. Here’s a detailed look at the typical CNC machining workflow:
1. Designing the Part
The process begins with creating a digital representation of the part using CAD software. Engineers and designers must ensure that the design meets all functional requirements and is optimized for manufacturing.
2. Programming the CNC Machine
Once the design is finalized, it is converted into a program that the CNC machine can understand, typically using CAM (Computer-Aided Manufacturing) software. This program dictates the tool paths and machining operations necessary to create the part.
3. Selecting the Material
The choice of material is critical. Depending on the part's intended use, manufacturers may select metals such as aluminum, steel, brass, or specialized alloys. Each material offers different properties such as strength, weight, and machinability.
4. Machining
During machining, the CNC machine uses various tools to cut, drill, and mill the selected material according to the programmed specifications. Tooling may include mills, lathes, and routers, each chosen based on the complexity of the part.
5. Finishing and Quality Control
Once machining is complete, parts undergo secondary processes such as deburring, polishing, and surface treatments to enhance their appearance and functionality. Quality control steps are implemented to ensure that each component meets dimensional and aesthetic standards.
6. Assembly and Packaging
In cases where the part is part of a larger assembly, skilled workers may assemble multiple components before packaging them for distribution. Effective packaging is vital to ensure parts arrive at their destination undamaged.
Applications of CNC Precision Machining Parts
CNC machining is used across various industries due to its versatility and precision. Here are some of the major applications:
- Aerospace: CNC parts are crucial in manufacturing components for aircraft, where reliability and precision are paramount.
- Automotive: The automotive industry utilizes CNC machining for everything from engine components to interior fittings.
- Medical: Customized parts for medical devices and equipment are often produced using CNC machining due to the strict accuracy requirements.
- Electronics: Precision components in consumer electronics, like housings and circuit boards, are frequently manufactured using CNC technologies.
- Defense: The defense industry requires high-precision parts for military equipment and machinery, benefitting from CNC precision machining.
Future Trends in CNC Precision Machining
The field of CNC precision machining is continually evolving, driven by advancements in technology and changing industry needs. Below are some trends shaping the future of CNC machining:
1. Automation and Robotics
The integration of robotics and automation in CNC machining is becoming increasingly common. This technology enhances efficiency and reduces human error, driving down costs and improving production speed.
2. Industry 4.0
As industries adopt Industry 4.0 principles, CNC machining is also integrating with smart technologies. Machines are becoming interconnected, facilitating real-time data monitoring and predictive maintenance, which leads to better performance and productivity.
3. Advanced Materials
The development of new materials with superior properties is influencing CNC machining as manufacturers seek to optimize performance in demanding applications. Innovations in composites and lightweight metals will open new avenues for CNC manufacturing.
4. Additive Manufacturing Integration
Combining CNC machining with additive manufacturing (3D printing) can produce complex parts more effectively. This hybrid approach allows manufacturers to leverage the strengths of both processes, creating parts that are lighter and stronger.
Conclusion
The significance of a cnc precision machining parts factory cannot be overstated in today's manufacturing landscape. With their ability to produce high-quality, precise components, CNC machining facilities, along with their team of skilled metal fabricators, are essential to advancing various industries. By staying at the forefront of technology and embracing new innovations, these factories will continue to meet the demands of the market, leading to an exciting future for precision machining.
As we move forward in this age of technology, understanding and leveraging the benefits of CNC precision machining will remain crucial for manufacturers aiming to establish a competitive edge. By investing in quality processes and skilled personnel, manufacturing businesses can ensure success in delivering superior products to their clients.