Understanding the Role of a Supplier Asphalt Mixing Plant in Modern Construction
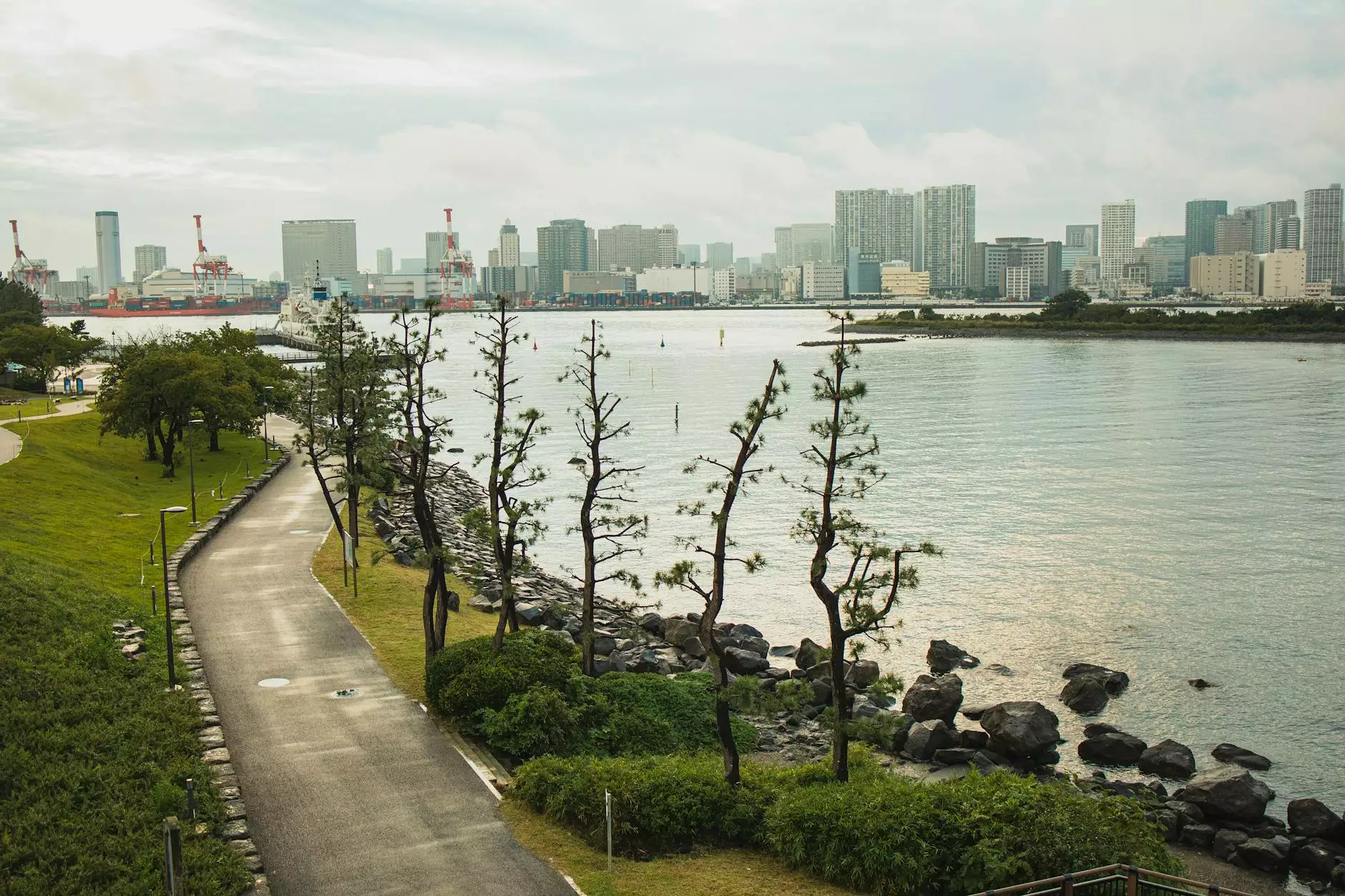
In the ever-evolving landscape of the construction industry, the role of specialized machinery has become indispensable. One such critical component is the supplier asphalt mixing plant. This article delves into the importance of these plants, their operational mechanics, various types, and their impact on the construction output and sustainability.
The Importance of Asphalt Mixing Plants
Asphalt mixing plants serve as the backbone of numerous construction projects, particularly in road construction and maintenance. Their function is to produce hot asphalt mixes that are essential for high-quality pavement. Here are several reasons why these plants are critical:
- Quality Assurance: A supplier asphalt mixing plant produces asphalt that meets stringent quality standards, ensuring durability and longevity.
- Efficiency: They allow for bulk production of asphalt, which speeds up the overall construction timeline.
- Cost-Effectiveness: By producing asphalt in facilities, construction companies can reduce costs associated with transportation and logistics.
- Environmental Control: Modern asphalt plants are designed with advanced technologies to recycle materials and reduce emissions, promoting greener construction practices.
Components of an Asphalt Mixing Plant
Understanding the components of a supplier asphalt mixing plant is crucial for appreciating its operation. Here are the core elements:
1. Cold Aggregate Supply System
This system is responsible for storing and transporting the raw aggregates to the mixing unit. It ensures the consistent feed of materials for optimal mixing.
2. Drying Drum
The drying drum removes moisture from the aggregates, which is vital for the proper bonding of asphalt. Efficient drying leads to a better quality mix.
3. Mixing Unit
This component combines the dried aggregates with bitumen and filler material. This is where the magic happens, as it results in a homogeneous asphalt mixture that conforms to the desired specifications.
4. Storage Silos
Storage silos are critical for holding the finished asphalt mixture until it is transported to the job site. They maintain the temperature of the asphalt, ensuring it remains workable.
5. Control System
Modern asphalt plants come equipped with sophisticated control systems that allow operators to monitor and adjust production parameters in real-time for maximum efficiency.
Types of Asphalt Mixing Plants
The choice of which asphalt mixing plant to utilize often depends on the specific requirements of the project. Here are the main types:
1. Batch Mix Plants
- Produce asphalt in batches.
- Allow for more precise control over the mix.
- Ideal for projects requiring high quality and varying specifications.
2. Continuous Mix Plants
- Produce asphalt continuously without interruption.
- More suited for larger projects with consistent demands.
- Generally more efficient for high-volume production needs.
3. Mobile Asphalt Plants
- Designed for easy transport between job sites.
- Great for temporary projects and reducing logistical costs.
- Flexibility in deployment makes them favorable for contractors.
Choosing the Right Supplier Asphalt Mixing Plant
Selecting the appropriate supplier asphalt mixing plant is crucial for the success of a construction project. Here are some factors to consider:
- Capacity: Assessing the daily production capacity required based on the project scope.
- Technology: Choosing a plant with the latest technology can enhance efficiency and reduce environmental impact.
- Quality Standards: Ensuring that the plant meets the necessary industry standards and certifications.
- Reputation: Researching the supplier’s track record can indicate reliability and customer service quality.
Impact of Asphalt Mixing Plants on Sustainability
As construction practices are increasingly scrutinized for their environmental impact, the role of asphalt mixing plants must be evaluated under this lens. Here’s how modern plants contribute to sustainability:
1. Recycling Capabilities
Modern supplier asphalt mixing plants can incorporate reclaimed asphalt pavement (RAP) into their mixes. This practice not only reduces waste but also conserves raw materials.
2. Lower Emissions
With advancements in technology, many plants are now able to significantly minimize emissions during production, helping to combat air pollution.
3. Energy Efficiency
New technologies allow plants to operate more energy-efficiently, reducing overall energy consumption in asphalt production.
Conclusion: The Future of Asphalt Mixing Plants
The future of construction relies heavily on the innovations within the industry, and supplier asphalt mixing plants are no exception. As demands for quality and sustainability continue to grow, the evolution of asphalt mixing technology will likely bring about even more efficient, environmentally friendly solutions. By investing in reliable and advanced asphalt mixing plants, construction companies can stay competitive in a challenging market, ensuring their projects are completed on time, within budget, and to the highest standards of quality.
Ultimately, the integration of cutting-edge asphalt mixing plants is more than just a trend; it is a reflection of the industry's commitment to sustainable practices and quality craftsmanship that will support infrastructure development for years to come.